Latest News: Participating again in Water, Energy, Technology & Environment Exhibition (WETEX-2024)
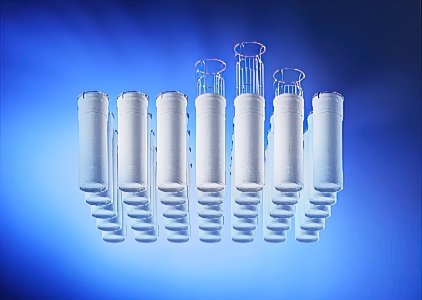
Supported Cages
Supporting cages and filter bags work together in the baghouse, with their interaction determining the efficiency of the baghouse and the service life of the filter bag. The filter bag and supporting cage must be optimally matched to each other to ensure a perfectly functioning baghouse. BWF Envirotec also supplies customers with matching supporting cages for all ready-made filter bags.
Types of Cages:
- Round or star-shaped for filter bags
- Flat for flat bags or filter bags
- Oval for oval filter bags
- Rectangular for filter bags
- Steel or stainless steel
Advantages:
- Cooperation with exclusive cage suppliers
- Steel and stainless-steel executions
- Customized designs and dimensions
- Wide selection of coatings for applications in a corrosive environment.
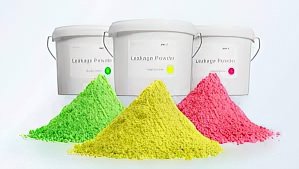
Leak Detection Powder / (Fluorescent Powder)
Leakage powder allows for leaks in filter bags and/or filter and extraction systems to be detected easily and effectively. To do so, fluorescent leakage powder is fed into the raw gas stream of the baghouse, then a UV lamp is used to inspect the filter medium for any trouble spots.
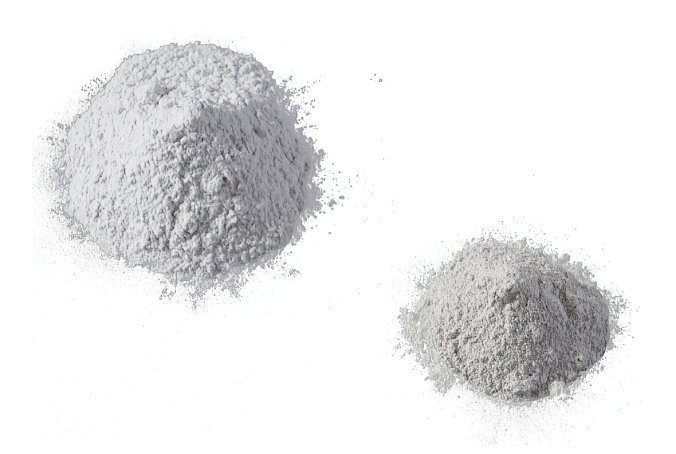
Pre-Coating Powder
Protection against watery and acidic condensations on the filter bags during start up
- Not for leakage test, but to protect the bags physically and chemically before start-up, precoating should be done.
- Without precoating, the virgin filter bags still have a high permeability. Due to the low flow resistance, the a/c ratio will be high during start-up, especially when the fan runs at full draft. Fine free flowing dust can cause immediate bleed-through and blinding of the bags.
- A precoating with good agglomerating dust reduces air permeability and initial a/c ratio and builds up a coherent dust cake, which protects the filter medium from dust penetration.
- When a combustion process is started up, vapour can condense in the still cold dust collector and form sulphuric acid. When hydrated lime Ca(OH)2 is used as a precoating, it will react and neutralize the acid, thus protecting the bags from chemical attack. But also unburned hydrocarbons will be separated on the dust cake and cannot penetrate the filter medium. Before precoating, the cleaning system should be turned off, to keep the dust cake on the bags until the regular operating conditions are reached.
- 200 g of hydrated lime Ca(OH)2 per 1 m² of filter area are sufficient for precoating. As a result of precoating, the differential pressure must increase at least by 3 – 4 mbar, otherwise the lime dust did not reach the filter bags but fell into the hopper.
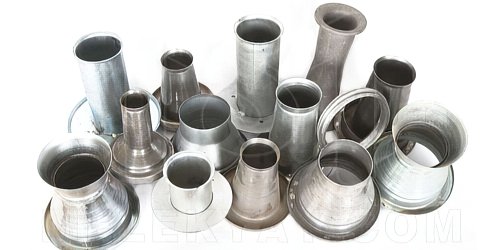
Venture
A venturi (or diffuser) is an integral component of certain pulse-jet manifolds. It conveys compressed air into the middle of the filter.
If the venturi is damaged or worn out, the compressed air does not achieve the speed required to effectively clean the filter bags, with the airflow being utilised in filtration systems to maintain high efficiency.
Types: Aluminum, pre-galvanized, stainless steel and ABS venturi.
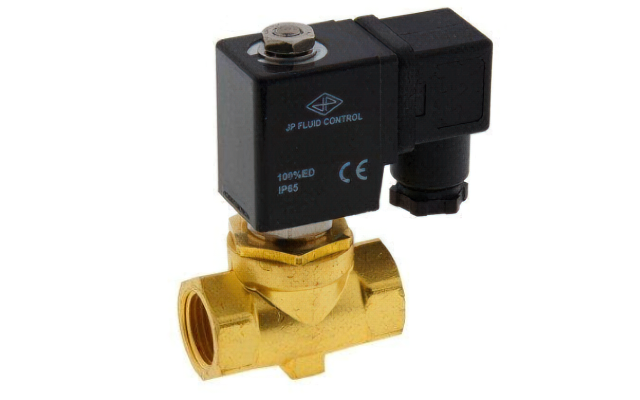
Solenoid Valves & Diaphram Kit
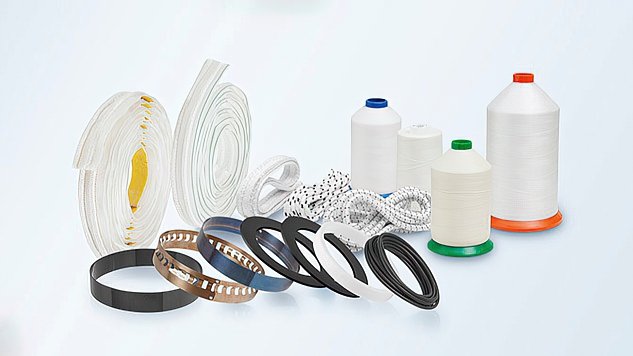